Plastronics: the benefits of a promising emerging technology
The potential for switches without mechanical parts is one of the most promising aspects of plastronics (also called IME - In-Mould Electronics). It is every design professional's dream to have a smooth, easy-to-clean surface that is simultaneously capable of incorporating capacitive elements, lighting and even haptic feedback and aerials. Today, we know that it is not a dream but an emerging technology that holds special value for some industries such as automotive or household appliances. We take a look at the enormous advantages of a way of working that Industrias Alegre has started incorporating into its operations and processes.
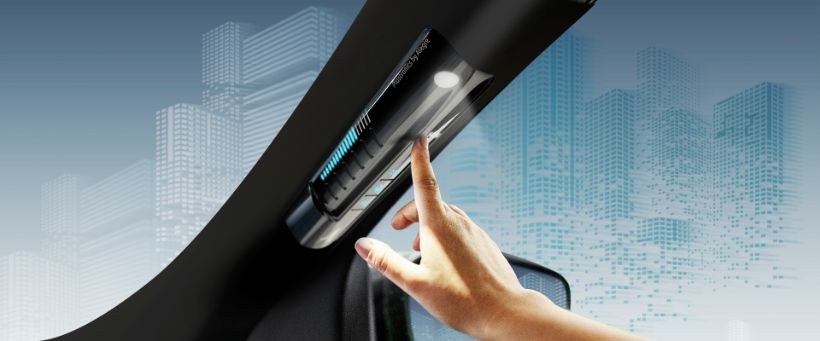
Strictly speaking, in-mould electronics is not a new technology, but a rather sophisticated evolution of injection moulding processes with decorative films - also called IMD (In-Mould Decoration). Integrating decorative films into moulded parts is a technique that has been used for years in a number of industries, including automotive. What is different about this formula (and its novel aspect) is that, while the decorative process combines three-dimensional moulding with films bearing the desired graphic element, the new process adds flexible elements with the desired electronics into the injected plastic with the aim of obtaining functioning parts.
Multiplying advantages
There are numerous benefits of adding electronics to a part from the mould, but within the industries in which Industrias Alegre works, we highlight the following six:
- By eliminating mechanical switches, both the number of parts and the complexity of the products are reduced.
- Assembly processes are eliminated during production and replaced by manufacturing processes.
- This technology makes it possible to integrate electronic elements into products and parts with structures and forms that would not easily accommodate mechanical elements.
- The thickness of parts can be reduced by up to 80% and weight can be reduced by up to 60%.
- More functionality can be offered in less space.
- The electronics are more durable because being integrated into the part means they are protected.
Aesthetic simplicity, as contemporary design demands; weight reduction, as electric cars require; functional grouping, as new users demand... If there are so many advantages, why aren't we already seeing more in-mould electronics?
The answer is obvious. Although incorporating an electronic film should be a process that is rather similar to that of integrating a decorative film, the reality is that there is a considerable difference, technically, between one and the other. Therefore, since the idea was launched on the market, significant technical challenges have needed to be overcome. And these have been resolved one after another.
From decorative films to flexible electronics
Most technical problems that have had to be solved are to do with the transition of a functional flexible film to three dimensions. The moulding of a plastic part causes changes that can be foreseen with a decorative film. However, these distortions can jeopardise the functioning of the electronics. And this has led experts to work in three areas:
- The choice of electronic materials, which need to withstand significant stretching and temperature increases without compromising subsequent operation.
- The structure and form of the part is also key, as the physical limits (minimum surfaces or curvatures) to which the electronic material can be taken need to be studied.
- To join the moulded part and the electronic film, the production process is critical and work has had to be done to ensure that the film is properly integrated and the resulting part is functional.
The challenges have now been overcome and, whilst in-mould electronics is still considered an emerging technology, it is very close to becoming a reality. And at Industrias Alegre that is what we are working towards.